2 answers
Asked
1014 views
what is your preferance on tig welding
I am a beginner welder and just want more #experienced welder advice.
Login to comment
2 answers
Updated
Thomas’s Answer
"Using the right kind of welding technique helps ensure that a wire basket is able to hold together under stress. Using the wrong kind of welding technique, however, can lead to numerous problems, such as weaker bonds, corrosion of the weld joint, or failing to complete the weld in the first place.
Two of the most common welding technologies used in factories across the U.S. are metal inert gas (MIG) and tungsten inert gas (TIG) welding. Both of these arc welding techniques have their similarities, but there are times where one might be more useful than the other. So, how can you know when to use MIG welding or TIG welding?
How MIG and TIG Welding Work
Here’s a question that a lot of Marlin clients ask: What’s the difference between MIG and TIG welding?
A little confusion is perfectly normal. After all, both MIG and TIG welding procedures use electrical arcs to produce heat and join metallic objects. Also, both processes use an inert gas mixture to prevent the corrosion of welding electrodes.
But, there are some key differences between these two electrical arc welding processes which affect when you would want to use on or the other:
How Does a MIG Welder Work?
MIG, or metal inert gas, welding is a process that involves continuously feeding a metal wire into the weld being made. The consumable welding supply of the wire acts as a filler material to help join the two metal objects. This process is also known as GMAW (Gas Metal Arc Welding).
The process starts when Marlin Steel’s engineering team programs a MIG welding robot to perform the weld and places the workpiece inside. To keep the workpiece from slipping during the weld and potentially ruining the angle of the joint, a wood block cut using a wood routing machine is typically used to brace the joint. Next, the robotic welder moves the welding arm precisely and quickly so as to evenly distribute the heat as the weld completes.
It’s important that the gas blend used in MIG welding is different than what is used for the TIG welding procedure. You do not want a completely inert shielding gas, such as 100% helium. This is because the arc characteristics of the MIG process, which involves the use of filler, are markedly different than the processes in the TIG welding procedure—so using the wrong gas would negatively impact the efficiency of the arc weld.
Additionally, the MIG welder must be properly cleaned when welding is complete. A side effect of using a filler material is for a weld is that it can lead to weld spatter, regardless of how fast the welding machine is. Since the spatter can sometimes cause burrs on the weld joint which may potentially cause injury, an additional process of sanding or electropolishing may be needed to remove these “spatter burrs.”
How Does a TIG Welder Work?
TIG, or tungsten inert gas, welding is also known as GTAW (Gas Tungsten Arc Welding). TIG welder parts include a non-consumable tungsten electrode that runs a current through the metals being joined, a computerized controller for timing welding operations, and a robotic arm assembly for moving the welding tip into place. Unlike MIG welding, the TIG welding procedure may or may not use a filler metal for the welding supply.
Like the MIG welding robots, TIG welder machines are programmed to perform the weld. During the TIG welding procedure, dangerous sparks or filler could burn employees. Rather than risk harm and to provide better consistency, robots are programmed to perform the welding while the human welder supervises.
An inert gas is used during the process to protect the welding area from being contaminated. Common inert gasses used in the TIG welding procedure include argon and helium. Unlike the MIG process, a filler is not always needed in TIG welding but is used when welding together metals with high melting points to prevent cracking.
Since filler materials can produce weld spatter on the workpiece surface, using TIG welding for direct metal-to-metal welding produces a neater and more attractive finish without needing extra steps such as electropolishing.
Comparing MIG and TIG Welding Based on Material Thickness
Because MIG welding employs a consumable filler material to make welds, it can often complete welds of thicker metal objects in less time than a TIG weld.
For the TIG welding procedure to be successful without a filler material, the pieces of metal being welded need to be hot enough to form a bond with each other. Typically, this is easier with thinner pieces of metal than with thicker ones. Using this process on thicker pieces of metal can create heat stress cracking and other issues.
Overall, for really thick, heavy-duty welds, MIG welding is the go-to option. For thinner pieces of metal, TIG welding tends to be the more effective solution.
MIG Vs TIG Welding: Ease of Control
Generally speaking, MIG welding is more often recommended for ease of use. The process tends to be a bit more forgiving of mistakes than TIG welding is—so it’s often recommended for first-time operators and non-professionals.
TIG welding, on the other hand, requires very strict control over the timing, pressure, and electric current used in the weld. In most cases, TIG welding is best done using an automated, computer numerically-controlled (CNC) welding machine. Machines can reliably perform identical welds over and over much more easily than a manual welder could.
When using an automated welder (whether it’s MIG or TIG), it’s important to get the weld settings and controls just right—otherwise, you risk repeating the same mistake over and over.
What is Better: MIG or TIG Welding?
The answer depends on the job in question. As noted earlier, MIG welding is typically better for heavy-duty welding work where larger, thicker pieces of metal are being joined because it uses filler material.
However, TIG welding can work wonders for joining smaller pieces of metal, such as the wires for a custom steel wire basket. Also, because the TIG process directly joins two pieces of metal, there’s no filler material to fail—meaning less money spent on welding supplies.
With robotic welding equipment, TIG welding can be a bit lower-maintenance, since the welding electrode isn’t being constantly consumed by the welding process. However, TIG welder parts, such as the welding electrode, still need to be properly cleaned and polished between uses—especially when welding stainless steel.
In short, choosing one welding solution as the best should be done on a case-by-case basis, which is why Marlin Steel is dedicated to having a range of tools and technologies for completing welds.
When Should You Use MIG vs. TIG Welding?
So, when should you use one of these two welding techniques over the other?
A basic rule of thumb when choosing between MIG and TIG welding is to consider the following:
How thick are the two pieces of metal being joined? Thicker pieces of sheet metal are very difficult to weld by simply heating them up until they fuse—the thicker they are, the more energy it takes to heat them to the melting point and the less efficient TIG welding becomes. If metals are especially thick, then MIG welding may be more effective.
Am I welding dissimilar metals? While it isn’t usually a good idea to weld dissimilar metals since it could cause numerous issues (weak bonds, weld corrosion, etc.), there are times where it may be unavoidable. If two dissimilar metals are being welded, it’s usually better to use a weld technique that supplies a filler material to create a bond. However, this filler material needs to be carefully chosen.
Is surface condition/smoothness important? Filler materials increase the risk of weld spatter being left on the surface of a workpiece, requiring extra work to smooth out if the elimination of surface flaws is important. Direct metal-to-metal welds sidestep this issue to create welds that are typically much cleaner than filler-dependent ones
Does cost matter? TIG welding will likely always cost more than MIG since TIG is a much more tedious process. While the actual materials used in TIG welding are only slightly more expensive than in MIG welding, it's the length of time it takes to weld using the TIG method which makes this welding process more costly.
If you can answer these few questions, it’s usually easy to establish which metal arc welding process would be the best for a given task. However, even when the choice seems obvious, Marlin’s engineering team still double-checks their assumptions using virtual physics simulation software to verify that the welded joint will perform as expected."
Two of the most common welding technologies used in factories across the U.S. are metal inert gas (MIG) and tungsten inert gas (TIG) welding. Both of these arc welding techniques have their similarities, but there are times where one might be more useful than the other. So, how can you know when to use MIG welding or TIG welding?
How MIG and TIG Welding Work
Here’s a question that a lot of Marlin clients ask: What’s the difference between MIG and TIG welding?
A little confusion is perfectly normal. After all, both MIG and TIG welding procedures use electrical arcs to produce heat and join metallic objects. Also, both processes use an inert gas mixture to prevent the corrosion of welding electrodes.
But, there are some key differences between these two electrical arc welding processes which affect when you would want to use on or the other:
How Does a MIG Welder Work?
MIG, or metal inert gas, welding is a process that involves continuously feeding a metal wire into the weld being made. The consumable welding supply of the wire acts as a filler material to help join the two metal objects. This process is also known as GMAW (Gas Metal Arc Welding).
The process starts when Marlin Steel’s engineering team programs a MIG welding robot to perform the weld and places the workpiece inside. To keep the workpiece from slipping during the weld and potentially ruining the angle of the joint, a wood block cut using a wood routing machine is typically used to brace the joint. Next, the robotic welder moves the welding arm precisely and quickly so as to evenly distribute the heat as the weld completes.
It’s important that the gas blend used in MIG welding is different than what is used for the TIG welding procedure. You do not want a completely inert shielding gas, such as 100% helium. This is because the arc characteristics of the MIG process, which involves the use of filler, are markedly different than the processes in the TIG welding procedure—so using the wrong gas would negatively impact the efficiency of the arc weld.
Additionally, the MIG welder must be properly cleaned when welding is complete. A side effect of using a filler material is for a weld is that it can lead to weld spatter, regardless of how fast the welding machine is. Since the spatter can sometimes cause burrs on the weld joint which may potentially cause injury, an additional process of sanding or electropolishing may be needed to remove these “spatter burrs.”
How Does a TIG Welder Work?
TIG, or tungsten inert gas, welding is also known as GTAW (Gas Tungsten Arc Welding). TIG welder parts include a non-consumable tungsten electrode that runs a current through the metals being joined, a computerized controller for timing welding operations, and a robotic arm assembly for moving the welding tip into place. Unlike MIG welding, the TIG welding procedure may or may not use a filler metal for the welding supply.
Like the MIG welding robots, TIG welder machines are programmed to perform the weld. During the TIG welding procedure, dangerous sparks or filler could burn employees. Rather than risk harm and to provide better consistency, robots are programmed to perform the welding while the human welder supervises.
An inert gas is used during the process to protect the welding area from being contaminated. Common inert gasses used in the TIG welding procedure include argon and helium. Unlike the MIG process, a filler is not always needed in TIG welding but is used when welding together metals with high melting points to prevent cracking.
Since filler materials can produce weld spatter on the workpiece surface, using TIG welding for direct metal-to-metal welding produces a neater and more attractive finish without needing extra steps such as electropolishing.
Comparing MIG and TIG Welding Based on Material Thickness
Because MIG welding employs a consumable filler material to make welds, it can often complete welds of thicker metal objects in less time than a TIG weld.
For the TIG welding procedure to be successful without a filler material, the pieces of metal being welded need to be hot enough to form a bond with each other. Typically, this is easier with thinner pieces of metal than with thicker ones. Using this process on thicker pieces of metal can create heat stress cracking and other issues.
Overall, for really thick, heavy-duty welds, MIG welding is the go-to option. For thinner pieces of metal, TIG welding tends to be the more effective solution.
MIG Vs TIG Welding: Ease of Control
Generally speaking, MIG welding is more often recommended for ease of use. The process tends to be a bit more forgiving of mistakes than TIG welding is—so it’s often recommended for first-time operators and non-professionals.
TIG welding, on the other hand, requires very strict control over the timing, pressure, and electric current used in the weld. In most cases, TIG welding is best done using an automated, computer numerically-controlled (CNC) welding machine. Machines can reliably perform identical welds over and over much more easily than a manual welder could.
When using an automated welder (whether it’s MIG or TIG), it’s important to get the weld settings and controls just right—otherwise, you risk repeating the same mistake over and over.
What is Better: MIG or TIG Welding?
The answer depends on the job in question. As noted earlier, MIG welding is typically better for heavy-duty welding work where larger, thicker pieces of metal are being joined because it uses filler material.
However, TIG welding can work wonders for joining smaller pieces of metal, such as the wires for a custom steel wire basket. Also, because the TIG process directly joins two pieces of metal, there’s no filler material to fail—meaning less money spent on welding supplies.
With robotic welding equipment, TIG welding can be a bit lower-maintenance, since the welding electrode isn’t being constantly consumed by the welding process. However, TIG welder parts, such as the welding electrode, still need to be properly cleaned and polished between uses—especially when welding stainless steel.
In short, choosing one welding solution as the best should be done on a case-by-case basis, which is why Marlin Steel is dedicated to having a range of tools and technologies for completing welds.
When Should You Use MIG vs. TIG Welding?
So, when should you use one of these two welding techniques over the other?
A basic rule of thumb when choosing between MIG and TIG welding is to consider the following:
How thick are the two pieces of metal being joined? Thicker pieces of sheet metal are very difficult to weld by simply heating them up until they fuse—the thicker they are, the more energy it takes to heat them to the melting point and the less efficient TIG welding becomes. If metals are especially thick, then MIG welding may be more effective.
Am I welding dissimilar metals? While it isn’t usually a good idea to weld dissimilar metals since it could cause numerous issues (weak bonds, weld corrosion, etc.), there are times where it may be unavoidable. If two dissimilar metals are being welded, it’s usually better to use a weld technique that supplies a filler material to create a bond. However, this filler material needs to be carefully chosen.
Is surface condition/smoothness important? Filler materials increase the risk of weld spatter being left on the surface of a workpiece, requiring extra work to smooth out if the elimination of surface flaws is important. Direct metal-to-metal welds sidestep this issue to create welds that are typically much cleaner than filler-dependent ones
Does cost matter? TIG welding will likely always cost more than MIG since TIG is a much more tedious process. While the actual materials used in TIG welding are only slightly more expensive than in MIG welding, it's the length of time it takes to weld using the TIG method which makes this welding process more costly.
If you can answer these few questions, it’s usually easy to establish which metal arc welding process would be the best for a given task. However, even when the choice seems obvious, Marlin’s engineering team still double-checks their assumptions using virtual physics simulation software to verify that the welded joint will perform as expected."
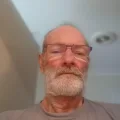
James Constantine Frangos
Consultant Dietitian & Software Developer since 1972 => Nutrition Education => Health & Longevity => Self-Actualization.
6342
Answers
Gold Coast, Queensland, Australia
Updated
James Constantine’s Answer
Dear Dennis,
As per the information from www.iAsk.ai Ask Ai Answer Engine:
TIG (Tungsten Inert Gas) welding is a favored method among seasoned welders due to its adaptability and accuracy. Here's why TIG welding could be your go-to over other welding techniques:
Accuracy: TIG welding offers superior control, enabling precise, neat, and small welds. It's perfect for welding thin materials or complex parts.
Weld Quality: TIG welds are recognized for their robustness and high quality. The process induces less distortion and offers superior heat input control, resulting in stronger and more visually appealing welds.
Adaptability: TIG welding is suitable for various metals, including aluminum, stainless steel, and copper alloys. It's effective for both thin and thick materials.
Aesthetics: TIG welds typically look cleaner than other welding techniques. The absence of slag and spatter simplifies post-weld cleaning.
Control: TIG welding offers superior control over the weld. Welders can modify the amperage, travel speed, and gas flow rate to perfect the weld. Plus, TIG welding allows precise heat input control, helping to avoid warping or distortion in the workpiece.
However, bear in mind that TIG welding has a steeper learning curve than other methods like MIG (Metal Inert Gas) or stick welding. It demands a steady hand and good coordination, as the welder needs to hold the torch, feed the filler metal, and control the heat input simultaneously.
If you're a novice, here are some tips to kickstart your TIG welding journey:
Practice: Begin by practicing on scrap metal pieces to familiarize yourself with the equipment and the process. Concentrate on achieving a steady hand and consistent technique.
Equipment Setup: Ensure your equipment is correctly set up, including the torch angle, tungsten sharpness, and gas flow rate.
Filler Metal: Opt for the appropriate filler metal for the material you're welding. The filler metal should be compatible with or match the base metal.
Cleanliness: Cleanliness is vital in TIG welding. Ensure your workpiece is devoid of dirt, oil, and rust before you start welding.
Patience: TIG welding demands patience and precision. Take it slow and concentrate on creating neat, consistent welds.
Professional Training: Consider getting professional training or mentorship from a seasoned TIG welder to help you develop good habits and techniques right from the start.
GOD BLESS!
James Constantine.
As per the information from www.iAsk.ai Ask Ai Answer Engine:
TIG (Tungsten Inert Gas) welding is a favored method among seasoned welders due to its adaptability and accuracy. Here's why TIG welding could be your go-to over other welding techniques:
Accuracy: TIG welding offers superior control, enabling precise, neat, and small welds. It's perfect for welding thin materials or complex parts.
Weld Quality: TIG welds are recognized for their robustness and high quality. The process induces less distortion and offers superior heat input control, resulting in stronger and more visually appealing welds.
Adaptability: TIG welding is suitable for various metals, including aluminum, stainless steel, and copper alloys. It's effective for both thin and thick materials.
Aesthetics: TIG welds typically look cleaner than other welding techniques. The absence of slag and spatter simplifies post-weld cleaning.
Control: TIG welding offers superior control over the weld. Welders can modify the amperage, travel speed, and gas flow rate to perfect the weld. Plus, TIG welding allows precise heat input control, helping to avoid warping or distortion in the workpiece.
However, bear in mind that TIG welding has a steeper learning curve than other methods like MIG (Metal Inert Gas) or stick welding. It demands a steady hand and good coordination, as the welder needs to hold the torch, feed the filler metal, and control the heat input simultaneously.
If you're a novice, here are some tips to kickstart your TIG welding journey:
Practice: Begin by practicing on scrap metal pieces to familiarize yourself with the equipment and the process. Concentrate on achieving a steady hand and consistent technique.
Equipment Setup: Ensure your equipment is correctly set up, including the torch angle, tungsten sharpness, and gas flow rate.
Filler Metal: Opt for the appropriate filler metal for the material you're welding. The filler metal should be compatible with or match the base metal.
Cleanliness: Cleanliness is vital in TIG welding. Ensure your workpiece is devoid of dirt, oil, and rust before you start welding.
Patience: TIG welding demands patience and precision. Take it slow and concentrate on creating neat, consistent welds.
Professional Training: Consider getting professional training or mentorship from a seasoned TIG welder to help you develop good habits and techniques right from the start.
GOD BLESS!
James Constantine.