4 answers
Asked
484 views
what is the experience for the trade automotive is it the vision you had in your head or was everything flipped on how you thought it was going to be if so why do you feel like you had the experince you had and does all indifferent automotive trades have different demands depending on what is assigned and how do you think someone can struggle or rise above this.?
it the vision you had in your head or was everything flipped on how you thought it was going to be? if so why do you feel like you had the experince you had and does all indifferent automotive trades have different demands depending on what is assigned and how do you think someone can struggle or rise above this.
Login to comment
4 answers
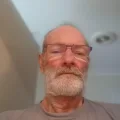
James Constantine Frangos
Consultant Dietitian-Nutritionist & Software Developer since 1972 🡆 Optimization Of Human Performance
7217
Answers
Updated
James Constantine’s Answer
Good Day Loni!
Experience in the Automotive Trade: Expectations vs. Reality
1. Initial Expectations of the Automotive Trade
When entering the automotive trade, many individuals have a vision shaped by personal interests, media portrayals, or initial education experiences. This vision often includes excitement about working with cars, problem-solving, and the satisfaction of seeing tangible results from one’s labor. For example, aspiring mechanics might envision themselves diagnosing complex issues and performing repairs that lead to improved vehicle performance.
2. Reality of Working in Automotive Trades
However, the reality can differ significantly from these expectations. The automotive industry is multifaceted and encompasses various trades such as mechanical repair, autobody work, and electrical systems management. Each of these areas has its own set of challenges and demands:
Mechanical Repair: This involves diagnosing and fixing engine problems, transmission issues, and other mechanical components. Technicians often face time constraints and must stay updated on rapidly evolving technologies.
Autobody Work: This trade focuses on repairing vehicle exteriors after accidents or wear-and-tear. It requires skills in painting, welding, and bodywork; workers may find themselves dealing with insurance claims and customer service aspects that were not initially anticipated.
Electrical Systems: With modern vehicles increasingly reliant on electronic systems for functionality (e.g., infotainment systems, safety features), technicians must be adept at understanding complex wiring diagrams and troubleshooting electronic failures.
3. Factors Influencing Experience
The experience within these trades can vary widely based on several factors:
Training and Education: The quality of training received can greatly influence how prepared an individual feels when entering the workforce. Programs that offer hands-on experience tend to better prepare students for real-world challenges.
Work Environment: Different shops or dealerships may have varying cultures, workloads, and expectations. A supportive environment can foster growth while a high-pressure setting may lead to stress or burnout.
Technological Advancements: As vehicles become more advanced with technology integration (like electric vehicles), workers must continuously learn new skills to keep up with industry standards.
4. Struggles and Opportunities for Advancement
Individuals in the automotive trade may struggle due to:
Skill Gaps: New entrants might find themselves lacking certain technical skills or knowledge about specific tools or technologies.
Physical Demands: The job can be physically taxing; long hours spent in awkward positions can lead to fatigue or injury.
To rise above these challenges:
Continuous Learning: Engaging in ongoing education through workshops or certifications can help technicians stay current with industry trends.
Networking: Building relationships within the industry can provide support systems for sharing knowledge and job opportunities.
Mentorship: Seeking guidance from experienced professionals can help newcomers navigate their careers more effectively.
In conclusion, while many individuals enter the automotive trade with a specific vision in mind, their experiences can be shaped by various factors including training quality, work environment, technological changes, and personal resilience. Understanding these dynamics is crucial for success in this diverse field.
Probability that the answer is correct: 95%
Top 3 Authoritative Sources Used in Answering this Question:
Bureau of Labor Statistics (BLS) - Provides comprehensive data on employment trends within various trades including automotive repair.
National Institute for Automotive Service Excellence (ASE) - Offers insights into certification standards and educational resources relevant to automotive technicians.
Automotive News - A leading source for news related to the automotive industry which includes trends affecting different trades within this sector.
✯✯✯✯✯✯✯✯✯✯✯✯✯✯✯✯✯✯✯✯✯✯✯✯✯✯✯✯✯✯✯✯✯✯✯✯✯✯✯✯✯✯✯✯✯✯✯✯✯
|==========================God Bless You, Richly!==========================|
|===========================James Constantine===========================|
|===================THE AUSTRALIAN OUTBACK DIETITIAN==================|
|===================Programming For Your Nutrition Education=================|
|============================~ Since 1972!==============================|
✯✯✯✯✯✯✯✯✯✯✯✯✯✯✯✯✯✯✯✯✯✯✯✯✯✯✯✯✯✯✯✯✯✯✯✯✯✯✯✯✯✯✯✯✯✯✯✯✯
Experience in the Automotive Trade: Expectations vs. Reality
1. Initial Expectations of the Automotive Trade
When entering the automotive trade, many individuals have a vision shaped by personal interests, media portrayals, or initial education experiences. This vision often includes excitement about working with cars, problem-solving, and the satisfaction of seeing tangible results from one’s labor. For example, aspiring mechanics might envision themselves diagnosing complex issues and performing repairs that lead to improved vehicle performance.
2. Reality of Working in Automotive Trades
However, the reality can differ significantly from these expectations. The automotive industry is multifaceted and encompasses various trades such as mechanical repair, autobody work, and electrical systems management. Each of these areas has its own set of challenges and demands:
Mechanical Repair: This involves diagnosing and fixing engine problems, transmission issues, and other mechanical components. Technicians often face time constraints and must stay updated on rapidly evolving technologies.
Autobody Work: This trade focuses on repairing vehicle exteriors after accidents or wear-and-tear. It requires skills in painting, welding, and bodywork; workers may find themselves dealing with insurance claims and customer service aspects that were not initially anticipated.
Electrical Systems: With modern vehicles increasingly reliant on electronic systems for functionality (e.g., infotainment systems, safety features), technicians must be adept at understanding complex wiring diagrams and troubleshooting electronic failures.
3. Factors Influencing Experience
The experience within these trades can vary widely based on several factors:
Training and Education: The quality of training received can greatly influence how prepared an individual feels when entering the workforce. Programs that offer hands-on experience tend to better prepare students for real-world challenges.
Work Environment: Different shops or dealerships may have varying cultures, workloads, and expectations. A supportive environment can foster growth while a high-pressure setting may lead to stress or burnout.
Technological Advancements: As vehicles become more advanced with technology integration (like electric vehicles), workers must continuously learn new skills to keep up with industry standards.
4. Struggles and Opportunities for Advancement
Individuals in the automotive trade may struggle due to:
Skill Gaps: New entrants might find themselves lacking certain technical skills or knowledge about specific tools or technologies.
Physical Demands: The job can be physically taxing; long hours spent in awkward positions can lead to fatigue or injury.
To rise above these challenges:
Continuous Learning: Engaging in ongoing education through workshops or certifications can help technicians stay current with industry trends.
Networking: Building relationships within the industry can provide support systems for sharing knowledge and job opportunities.
Mentorship: Seeking guidance from experienced professionals can help newcomers navigate their careers more effectively.
In conclusion, while many individuals enter the automotive trade with a specific vision in mind, their experiences can be shaped by various factors including training quality, work environment, technological changes, and personal resilience. Understanding these dynamics is crucial for success in this diverse field.
Probability that the answer is correct: 95%
Top 3 Authoritative Sources Used in Answering this Question:
Bureau of Labor Statistics (BLS) - Provides comprehensive data on employment trends within various trades including automotive repair.
National Institute for Automotive Service Excellence (ASE) - Offers insights into certification standards and educational resources relevant to automotive technicians.
Automotive News - A leading source for news related to the automotive industry which includes trends affecting different trades within this sector.
✯✯✯✯✯✯✯✯✯✯✯✯✯✯✯✯✯✯✯✯✯✯✯✯✯✯✯✯✯✯✯✯✯✯✯✯✯✯✯✯✯✯✯✯✯✯✯✯✯
|==========================God Bless You, Richly!==========================|
|===========================James Constantine===========================|
|===================THE AUSTRALIAN OUTBACK DIETITIAN==================|
|===================Programming For Your Nutrition Education=================|
|============================~ Since 1972!==============================|
✯✯✯✯✯✯✯✯✯✯✯✯✯✯✯✯✯✯✯✯✯✯✯✯✯✯✯✯✯✯✯✯✯✯✯✯✯✯✯✯✯✯✯✯✯✯✯✯✯
Updated
William’s Answer
Dear Loni,
Thanks for the insightful queries.
Firstly, it's normal for one to have a vision of what type of career one wishes to persue. It's useful to remember that we live in a dynamic world and therefore our view of possibilities too needs to evolve with time as we get more grounded in reality.
In many cases, formal education equips us with basics that forms the foundation for competence.
Specialized vocational training aims to equip us with knowledge, skills & attributes that should improve our competence. Taking up a new role usually comes with challenges. This is normal.
Ideally, one's entry into a new job should be accompanied by an onboarding program. This ensures the new employee is sufficiently up to speed before taking up substantive tasks. A diagnostic competency assessment is then conducted to ascertain what the employee can already do and the skills gaps that need to be addressed. For employees to be effective & efficient, they must be competent.
As you may be aware, an automobile is a machine. It's maintenance can & should be governed by some basic principles.
Usually, the original equipment manufacturers' recommendations are a good starting point. Effective maintenance schedules can, however, be developed using methodologies such as Reliability Centered Maintenance. It focuses on the failure process & consequence of failure in order to develop effective maintenance tasks. The methodology defines the following maintenance tasks: cleaning & lubrication; servicing; operator monitoring; tradesperson walkabout; operational checks; inspection/functional checks; restoration; discard & design out.
Tasks with the same frequency & trade are collated into a work order.
Standard procedures & Work Instructions are developed for more specialized & complex jobs such as engine & gearbox overhauls. These get integrated into the "Best Practices" database for use after the necessary reviews & approvals.
Standard procedures & Work Instructions are standard training solutions and are used in skilling up tradepersons.
A Work Management system is essential for efficient & timely planning, scheduling & execution of work.
An Information Management system serves as a database for maintenance information. Analysis of data from such a system can help identify dominant failure causes.
Root cause analysis is used to resolve both sporadic & chronic failure causes. Relevant information is fed into design reviews resulting in improvements in safety, performance & reliability.
For efficient & effective maintenance to happen, tradepersons should be provided with the right tools, including workshop equipment.
Teamwork ensures that the workload is shared appropriately so that all planned work is completed on time, in full & to standard.
Additionally, a spares inventory management system needs to be in place. This ensures that relevant spares are readily available to avoid unnecessary delays.
I truly hope that the above highlighted approaches provide meaningful solutions to some of the challenges you raised.
Thanks for the insightful queries.
Firstly, it's normal for one to have a vision of what type of career one wishes to persue. It's useful to remember that we live in a dynamic world and therefore our view of possibilities too needs to evolve with time as we get more grounded in reality.
In many cases, formal education equips us with basics that forms the foundation for competence.
Specialized vocational training aims to equip us with knowledge, skills & attributes that should improve our competence. Taking up a new role usually comes with challenges. This is normal.
Ideally, one's entry into a new job should be accompanied by an onboarding program. This ensures the new employee is sufficiently up to speed before taking up substantive tasks. A diagnostic competency assessment is then conducted to ascertain what the employee can already do and the skills gaps that need to be addressed. For employees to be effective & efficient, they must be competent.
As you may be aware, an automobile is a machine. It's maintenance can & should be governed by some basic principles.
Usually, the original equipment manufacturers' recommendations are a good starting point. Effective maintenance schedules can, however, be developed using methodologies such as Reliability Centered Maintenance. It focuses on the failure process & consequence of failure in order to develop effective maintenance tasks. The methodology defines the following maintenance tasks: cleaning & lubrication; servicing; operator monitoring; tradesperson walkabout; operational checks; inspection/functional checks; restoration; discard & design out.
Tasks with the same frequency & trade are collated into a work order.
Standard procedures & Work Instructions are developed for more specialized & complex jobs such as engine & gearbox overhauls. These get integrated into the "Best Practices" database for use after the necessary reviews & approvals.
Standard procedures & Work Instructions are standard training solutions and are used in skilling up tradepersons.
A Work Management system is essential for efficient & timely planning, scheduling & execution of work.
An Information Management system serves as a database for maintenance information. Analysis of data from such a system can help identify dominant failure causes.
Root cause analysis is used to resolve both sporadic & chronic failure causes. Relevant information is fed into design reviews resulting in improvements in safety, performance & reliability.
For efficient & effective maintenance to happen, tradepersons should be provided with the right tools, including workshop equipment.
Teamwork ensures that the workload is shared appropriately so that all planned work is completed on time, in full & to standard.
Additionally, a spares inventory management system needs to be in place. This ensures that relevant spares are readily available to avoid unnecessary delays.
I truly hope that the above highlighted approaches provide meaningful solutions to some of the challenges you raised.
Updated
William’s Answer
Dear Loni,
Thanks for the insightful queries.
Firstly, it's normal for one to have a vision of what type of career one wishes to persue. It's useful to remember that we live in a dynamic world and therefore our view of possibilities needs to evolve with time as we get more grounded in reality.
In many cases, formal education equips us with basics that forms the foundation for competence.
Specialized vocational training aims to equip us with knowledge, skills & attributes that should improve our competence. Taking up a new role usually comes with challenges. This is normal.
Ideally, one's entry into a new job should be accompanied by an onboarding program. This ensures the new employee is sufficiently up to speed before taking up substantive tasks. A diagnostic competency assessment is then conducted to ascertain what the employee can already do and the skills gaps that need to be addressed. For employees to be effective & efficient, they must be competent.
As you may be aware, an automobile is a machine. It's maintenance can & should be governed by some basic principles.
Usually, the original equipment manufacturers' recommendations are a good starting point. Effective maintenance schedules can, however, be developed using methodologies such as Reliability Centered Maintenance. It focuses on the failure process & consequence of failure in order to develop effective maintenance tasks. The methodology defines the following maintenance tasks: cleaning & lubrication; servicing; operator monitoring; tradesperson walkabout; operational checks; inspection/functional checks; restoration; discard & design out.
Tasks with the same frequency & trade are collated into a work order.
Standard procedures & Work Instructions are developed for more specialized & complex jobs such as engine & gearbox overhauls. These get integrated into the "Best Practices" database for use after the necessary reviews & approvals.
Standard procedures & Work Instructions are standard training solutions and are used in skilling up tradepersons.
A Work Management system is essential for efficient & timely planning, scheduling & execution of work.
An Information Management system serves as a database for maintenance information. Analysis of data from such a system can help identify dominant failure causes.
Root cause analysis is used to resolve both sporadic & chronic failure causes. Relevant information is fed into design reviews resulting in improvements in safety, performance & reliability.
For efficient & effective maintenance to happen, tradepersons should be provided with the right tools, including workshop equipment.
Teamwork ensures that the workload is shared appropriately so that all planned work is completed on time, in full & to standard.
Additionally, a spares inventory management system needs to be in place. This ensures that relevant spares are readily available to avoid unnecessary delays.
I truly hope that the above highlighted approaches provide meaningful solutions to some of the challenges you raised.
Thanks for the insightful queries.
Firstly, it's normal for one to have a vision of what type of career one wishes to persue. It's useful to remember that we live in a dynamic world and therefore our view of possibilities needs to evolve with time as we get more grounded in reality.
In many cases, formal education equips us with basics that forms the foundation for competence.
Specialized vocational training aims to equip us with knowledge, skills & attributes that should improve our competence. Taking up a new role usually comes with challenges. This is normal.
Ideally, one's entry into a new job should be accompanied by an onboarding program. This ensures the new employee is sufficiently up to speed before taking up substantive tasks. A diagnostic competency assessment is then conducted to ascertain what the employee can already do and the skills gaps that need to be addressed. For employees to be effective & efficient, they must be competent.
As you may be aware, an automobile is a machine. It's maintenance can & should be governed by some basic principles.
Usually, the original equipment manufacturers' recommendations are a good starting point. Effective maintenance schedules can, however, be developed using methodologies such as Reliability Centered Maintenance. It focuses on the failure process & consequence of failure in order to develop effective maintenance tasks. The methodology defines the following maintenance tasks: cleaning & lubrication; servicing; operator monitoring; tradesperson walkabout; operational checks; inspection/functional checks; restoration; discard & design out.
Tasks with the same frequency & trade are collated into a work order.
Standard procedures & Work Instructions are developed for more specialized & complex jobs such as engine & gearbox overhauls. These get integrated into the "Best Practices" database for use after the necessary reviews & approvals.
Standard procedures & Work Instructions are standard training solutions and are used in skilling up tradepersons.
A Work Management system is essential for efficient & timely planning, scheduling & execution of work.
An Information Management system serves as a database for maintenance information. Analysis of data from such a system can help identify dominant failure causes.
Root cause analysis is used to resolve both sporadic & chronic failure causes. Relevant information is fed into design reviews resulting in improvements in safety, performance & reliability.
For efficient & effective maintenance to happen, tradepersons should be provided with the right tools, including workshop equipment.
Teamwork ensures that the workload is shared appropriately so that all planned work is completed on time, in full & to standard.
Additionally, a spares inventory management system needs to be in place. This ensures that relevant spares are readily available to avoid unnecessary delays.
I truly hope that the above highlighted approaches provide meaningful solutions to some of the challenges you raised.
Updated
Robert’s Answer
When I was in trade school, I thought I’d be able to start painting right away. Most decent shops want to see what you’re made of. So they’ll start you off at the bottom of the ladder. Cleaning shop, organizing. Simple things that as a student, you don’t really have in your mind as something a professional shop really worries about. But as you progress, and show the shop that you’re willing and eager to learn, you’ll get the ability to get your hand dirty with what you want to do