4 answers
4 answers
Updated
naveen’s Answer
What types of welding are available?
• Arc welding: Employees often use this type of welding when working in construction and manufacturing to weld larger and thicker materials together. It's also referred to as "stick welding" and involves basic fusion practices.
• MIG welding: As one of the most popular welding practices, MIG welding involves fusing stainless steel, mild steel and aluminum. Many consider this the simplest type of welding to learn. Many employers will require welders to know this type of welding.
• TIG welding: This is one of the more complex welding types to learn. It uses tungsten inert gas to create fusions that are considered more high-quality than others. This welding type often requires higher-level education, training or certifications.
• Hyperbaric welding: Hyperbaric welding can be conducted in a dry environment, but the same method can be used when welding underwater. Workers who learn this specific type of welding can work on ships, pipelines and oil platforms.
• Oxyacetylene welding: Steel melts from this type of welding using acetylene gas and oxygen. It can be used for maintenance or cutting of various metal types.
• Arc welding: Employees often use this type of welding when working in construction and manufacturing to weld larger and thicker materials together. It's also referred to as "stick welding" and involves basic fusion practices.
• MIG welding: As one of the most popular welding practices, MIG welding involves fusing stainless steel, mild steel and aluminum. Many consider this the simplest type of welding to learn. Many employers will require welders to know this type of welding.
• TIG welding: This is one of the more complex welding types to learn. It uses tungsten inert gas to create fusions that are considered more high-quality than others. This welding type often requires higher-level education, training or certifications.
• Hyperbaric welding: Hyperbaric welding can be conducted in a dry environment, but the same method can be used when welding underwater. Workers who learn this specific type of welding can work on ships, pipelines and oil platforms.
• Oxyacetylene welding: Steel melts from this type of welding using acetylene gas and oxygen. It can be used for maintenance or cutting of various metal types.
Updated
Hiep’s Answer
Hi Jonathan,
I had three years working in a steam boiler company and manage a team of welders.
To be a good welder, you should go through training courses providing during your colleague schools or technical training school. It's normal to take three to six months for fundamental welding on simple/normal steel structures. Another 1-2 years so that you can become a higher senior welder who can work on a high-pressure piping system or oil piping system.
You should be a very skillful person as welding normally involve health and safety risks such as electric shock, falling from a height, lack of oxygen when working in confined space. So that trickly follow safety procedure and good safety awareness of safety risks are critical for you.
You also need to be very strong and healthy as these works will require you to work with heavy objects. Teamworks is another skill that you need to learn as you will need to cooperate with others during projects.
In addition, the capability to read and understand technical drawings so that you can perform your works as required.
Just let me know if you need more clarification.
I hope that helps!
I had three years working in a steam boiler company and manage a team of welders.
To be a good welder, you should go through training courses providing during your colleague schools or technical training school. It's normal to take three to six months for fundamental welding on simple/normal steel structures. Another 1-2 years so that you can become a higher senior welder who can work on a high-pressure piping system or oil piping system.
You should be a very skillful person as welding normally involve health and safety risks such as electric shock, falling from a height, lack of oxygen when working in confined space. So that trickly follow safety procedure and good safety awareness of safety risks are critical for you.
You also need to be very strong and healthy as these works will require you to work with heavy objects. Teamworks is another skill that you need to learn as you will need to cooperate with others during projects.
In addition, the capability to read and understand technical drawings so that you can perform your works as required.
Just let me know if you need more clarification.
I hope that helps!
Updated
naveen’s Answer
What types of welding are available
• Arc welding: Employees often use this type of welding when working in construction and manufacturing to weld larger and thicker materials together. It's also referred to as "stick welding" and involves basic fusion practices.
• MIG welding: As one of the most popular welding practices, MIG welding involves fusing stainless steel, mild steel and aluminum. Many consider this the simplest type of welding to learn. Many employers will require welders to know this type of welding.
• TIG welding: This is one of the more complex welding types to learn. It uses tungsten inert gas to create fusions that are considered more high-quality than others. This welding type often requires higher-level education, training or certifications.
• Hyperbaric welding: Hyperbaric welding can be conducted in a dry environment, but the same method can be used when welding underwater. Workers who learn this specific type of welding can work on ships, pipelines and oil platforms.
• Oxyacetylene welding: Steel melts from this type of welding using acetylene gas and oxygen. It can be used for maintenance or cutting of various metal types.
• Arc welding: Employees often use this type of welding when working in construction and manufacturing to weld larger and thicker materials together. It's also referred to as "stick welding" and involves basic fusion practices.
• MIG welding: As one of the most popular welding practices, MIG welding involves fusing stainless steel, mild steel and aluminum. Many consider this the simplest type of welding to learn. Many employers will require welders to know this type of welding.
• TIG welding: This is one of the more complex welding types to learn. It uses tungsten inert gas to create fusions that are considered more high-quality than others. This welding type often requires higher-level education, training or certifications.
• Hyperbaric welding: Hyperbaric welding can be conducted in a dry environment, but the same method can be used when welding underwater. Workers who learn this specific type of welding can work on ships, pipelines and oil platforms.
• Oxyacetylene welding: Steel melts from this type of welding using acetylene gas and oxygen. It can be used for maintenance or cutting of various metal types.
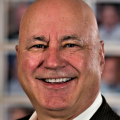
Michael J. Kotubey, LEED AP
Senior Management - Operations, Sales, Marketing, Business Development
3
Answers
Keller, Texas
Updated
Michael J.’s Answer
It would depend on your specialty. Two focus areas are structural welding and pipefitting/pipe welding. A third is robotic welding which is typically used in manufacturing.
All teach physical welding techniques such as how to use various welding processes, gases and equipment. They also teach material composition so that the right processes and tools are used. They also teach safety - physical and environmental.
Structural welding and pipefitting use extensive math and geometry. Rigging and materials set up are also taught. In robotics you are taught how to operate and how to program a robot to achieve the desired result.
All teach physical welding techniques such as how to use various welding processes, gases and equipment. They also teach material composition so that the right processes and tools are used. They also teach safety - physical and environmental.
Structural welding and pipefitting use extensive math and geometry. Rigging and materials set up are also taught. In robotics you are taught how to operate and how to program a robot to achieve the desired result.