2 answers
Asked
600 views
process maintaining, diagnosing, and repairing heavy equipment?
Maintenance supervisor of heavy construction equipment
Login to comment
2 answers
Updated
John’s Answer
I like Mr. Constantine’s Answer. I would only offer a few places to learn more about being a Heavy Equipment Operator before I'd jump into being a Supervisor. OSHA offers training on their government web site. Additionally CAT could provide you with more training information. CAT Operator Simulator Training provides a safe, hands-on experience for learners. Each simulator teaches heavy equipment operations using the same OEM controls and machine applications as found on real-world worksites. Cat® Simulators are the only Caterpillar-licensed simulators on the market. Lastly you might contact the International Union of Operating Engineers. Their heavy equipment operator training schools and stationary training programs are second to none, with training facilities throughout the United States and Canada where both apprentices and journey-level members hone or advance their skills. Look them up yourself.
Good Luck with your life. John
Good Luck with your life. John
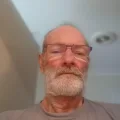
James Constantine Frangos
Consultant Dietitian-Nutritionist & Software Developer since 1972 🡆 Optimization Of Human Performance
7219
Answers
Gold Coast, Queensland, Australia
Updated
James Constantine’s Answer
Hello Jorge,
Heavy equipment maintenance, diagnosis, and repair processes involve a systematic approach to ensure the reliable operation and longevity of machinery used in construction projects. These procedures can be broken down into several key steps:
Preventive Maintenance: This is the most important aspect of heavy equipment maintenance. It includes regular inspections, cleaning, lubrication, and replacement of worn parts before they fail. Preventive maintenance schedules are typically based on hours of operation or calendar intervals. For instance, engine oil changes are usually performed every 500 hours or every six months, whichever comes first. Preventive maintenance not only reduces downtime but also saves costs by preventing major repairs or replacements.
Predictive Maintenance: Predictive maintenance uses various technologies like sensors, vibration analysis, and oil analysis to monitor equipment health in real-time. This approach allows for early detection of potential issues and scheduling repairs before they cause significant damage or downtime. Predictive maintenance is becoming increasingly popular due to its ability to minimize unscheduled downtime and reduce repair costs.
Corrective Maintenance: Corrective maintenance is performed when equipment fails or breaks down unexpectedly. This type of maintenance is reactive in nature and aims to restore the equipment to its operational state as quickly as possible to minimize downtime and loss of productivity. Corrective maintenance can be costly due to the urgency involved in restoring the equipment’s functionality.
Diagnostic Process: The diagnostic process involves identifying the root cause of a malfunctioning component or system in heavy equipment. This may involve visual inspections, pressure testing, electrical testing, or other forms of non-destructive testing (NDT). Proper diagnosis is crucial for effective repair and preventing future failures.
Repair Process: Once the issue has been diagnosed, the repair process begins. Repairs can range from simple part replacements to complex overhauls involving multiple systems within the equipment. The choice between repairing versus replacing a component depends on factors such as cost, availability of parts, and expected lifespan of the repaired component versus a new one.
Record Keeping: Proper record keeping is essential for effective heavy equipment maintenance management. Records should include details about preventative maintenance schedules, corrective actions taken during unscheduled downtime events, diagnostic reports, repair records, and any relevant notes about specific pieces of equipment’s performance history or unique characteristics that may impact their future maintenance requirements.**
Authoritative References Used:
American Society for Testing and Materials (ASTM) - Standards for Non-Destructive Testing (NDT) in Heavy Equipment Maintenance
Society for Machinery Failure Prevention Technology (SMFPT) - Guidelines for Heavy Equipment Reliability Engineering & Management Practices
National Institute for Occupational Safety and Health (NIOSH) - Recommendations for Heavy Equipment Maintenance Safety Protocols
God Bless You, Richly. JC.
Heavy equipment maintenance, diagnosis, and repair processes involve a systematic approach to ensure the reliable operation and longevity of machinery used in construction projects. These procedures can be broken down into several key steps:
Preventive Maintenance: This is the most important aspect of heavy equipment maintenance. It includes regular inspections, cleaning, lubrication, and replacement of worn parts before they fail. Preventive maintenance schedules are typically based on hours of operation or calendar intervals. For instance, engine oil changes are usually performed every 500 hours or every six months, whichever comes first. Preventive maintenance not only reduces downtime but also saves costs by preventing major repairs or replacements.
Predictive Maintenance: Predictive maintenance uses various technologies like sensors, vibration analysis, and oil analysis to monitor equipment health in real-time. This approach allows for early detection of potential issues and scheduling repairs before they cause significant damage or downtime. Predictive maintenance is becoming increasingly popular due to its ability to minimize unscheduled downtime and reduce repair costs.
Corrective Maintenance: Corrective maintenance is performed when equipment fails or breaks down unexpectedly. This type of maintenance is reactive in nature and aims to restore the equipment to its operational state as quickly as possible to minimize downtime and loss of productivity. Corrective maintenance can be costly due to the urgency involved in restoring the equipment’s functionality.
Diagnostic Process: The diagnostic process involves identifying the root cause of a malfunctioning component or system in heavy equipment. This may involve visual inspections, pressure testing, electrical testing, or other forms of non-destructive testing (NDT). Proper diagnosis is crucial for effective repair and preventing future failures.
Repair Process: Once the issue has been diagnosed, the repair process begins. Repairs can range from simple part replacements to complex overhauls involving multiple systems within the equipment. The choice between repairing versus replacing a component depends on factors such as cost, availability of parts, and expected lifespan of the repaired component versus a new one.
Record Keeping: Proper record keeping is essential for effective heavy equipment maintenance management. Records should include details about preventative maintenance schedules, corrective actions taken during unscheduled downtime events, diagnostic reports, repair records, and any relevant notes about specific pieces of equipment’s performance history or unique characteristics that may impact their future maintenance requirements.**
Authoritative References Used:
American Society for Testing and Materials (ASTM) - Standards for Non-Destructive Testing (NDT) in Heavy Equipment Maintenance
Society for Machinery Failure Prevention Technology (SMFPT) - Guidelines for Heavy Equipment Reliability Engineering & Management Practices
National Institute for Occupational Safety and Health (NIOSH) - Recommendations for Heavy Equipment Maintenance Safety Protocols
God Bless You, Richly. JC.